The CAN bus system is essential in modern vehicles and various automated systems. It allows different electronic control units to communicate efficiently and reliably with minimal wiring.
With over 20 years of combined experience in the field, our team has a deep understanding of the CAN bus system.
In this guide, we'll break down the CAN bus system into simple terms, covering its basics, components, and how it works. Whether you're new to the topic or need a refresher, you'll find this information clear and helpful.
What is CAN bus?
The Controller Area Network (CAN) bus is a robust vehicle bus standard designed to allow microcontrollers and devices to communicate with each other without a host computer. Originally developed by Bosch in the mid-1980s, it has become a fundamental technology in modern vehicles and various automated systems.
-
Controller Area Network (CAN):
-
Controller: This refers to the different parts or devices that need to communicate, like sensors or control units.
-
Area Network: This is the network connecting these controllers, allowing them to share information.
-
-
Bus:
-
Think of bus as a pathway. Just like a bus on the road picks up and drops off passengers at various stops, the CAN bus protocol transports messages between different parts of a machine.
-
The development of the CAN bus system was driven by the need to simplify the increasingly complex wiring systems in vehicles. Before its introduction, each function in a vehicle required a dedicated point-to-point wiring system, resulting in a tangled mass of wires. In 1986, Bosch introduced the CAN bus, significantly reducing the wiring required, simplifying vehicle design, and improving overall reliability.
Why is CAN bus important?
CAN bus is crucial because it simplifies the way machines and vehicles operate. By using a single communication system, it:
-
Reduces wiring complexity:
-
Minimizing the number of cables needed for communication.
-
-
Lowers costs:
-
Fewer wires mean lower manufacturing and maintenance costs.
-
-
Improves reliability:
-
Fewer connections mean fewer potential failure points.
-
-
-
Ensures faster and more efficient data exchange between components.
-
This efficiency has made CAN bus indispensable not only in automotive applications but also in industrial automation, medical equipment, and other fields requiring robust, real-time communication.
"CAN bus protocol might sound complex at first, but it’s essentially a robust and streamlined way for different parts of a machine to communicate. It’s like having a well-organized conversation where everyone gets a chance to speak and listen, ensuring smooth operation."
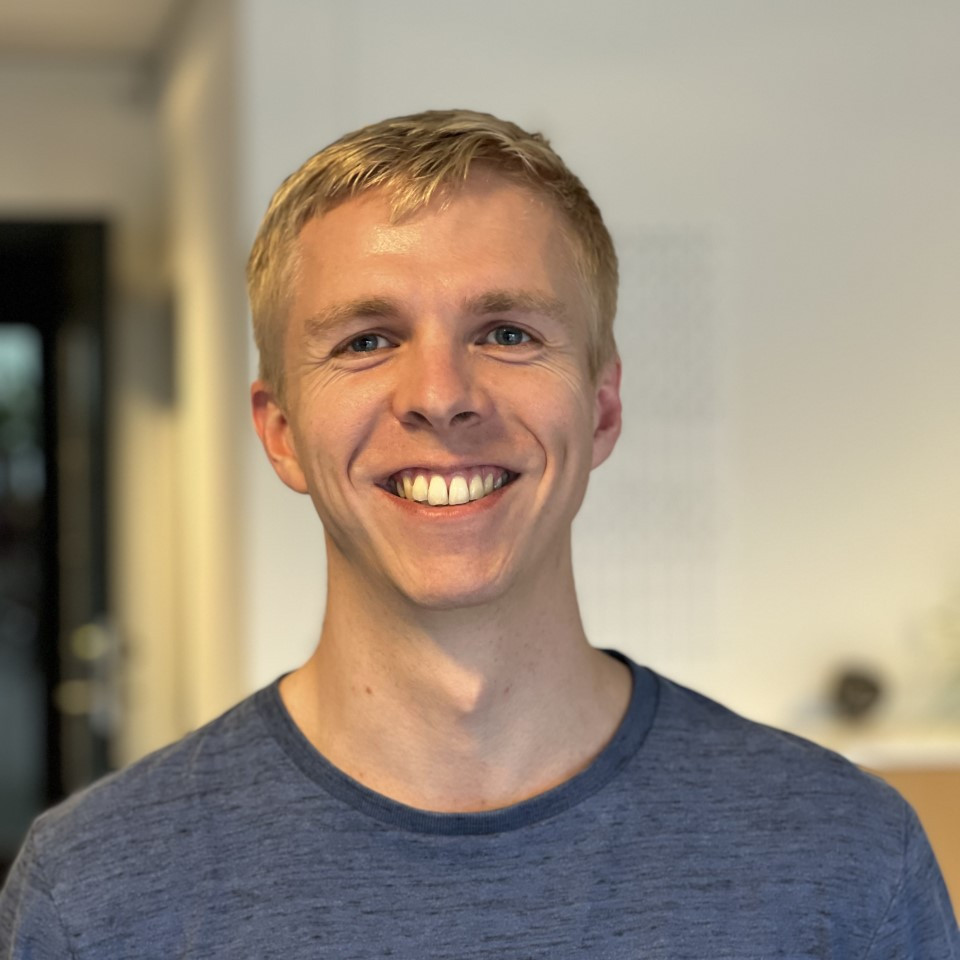
Real-world example:
Think about your car’s braking system. When you press the brake pedal, the CAN bus protocol sends a message from the pedal sensor to the brake lights, anti-lock braking system (ABS), and other components. This ensures everything responds correctly and simultaneously, making your driving experience safer and more reliable.
The CAN bus system’s versatility has led to its widespread adoption beyond automotive applications, finding use in industrial automation, medical equipment, and other fields that require robust and efficient communication protocols. From reducing complex wiring to enhancing real-time communication, the CAN bus system has transformed how machines and vehicles operate—setting the standard for modern, efficient, and reliable technology.
Why is CAN bus Important?
Understanding why the CAN bus protocol matters can help you appreciate how it makes everyday technology more reliable and efficient.
Before CAN bus, vehicles and machines used a lot of individual wires to connect each component. This made systems bulky, complicated, and prone to errors. CAN bus reduces this complexity by allowing multiple devices to share a single communication pathway.
CAN bus enhances the reliability of communication between different parts of a system. Because it uses fewer wires and a standardized protocol, there are fewer points of failure. This means that machines and vehicles are less likely to experience issues and are easier to maintain.
"CAN bus has changed the game. It makes communication between parts of a system much simpler and more reliable. This improvement has pushed many industries forward in big ways."
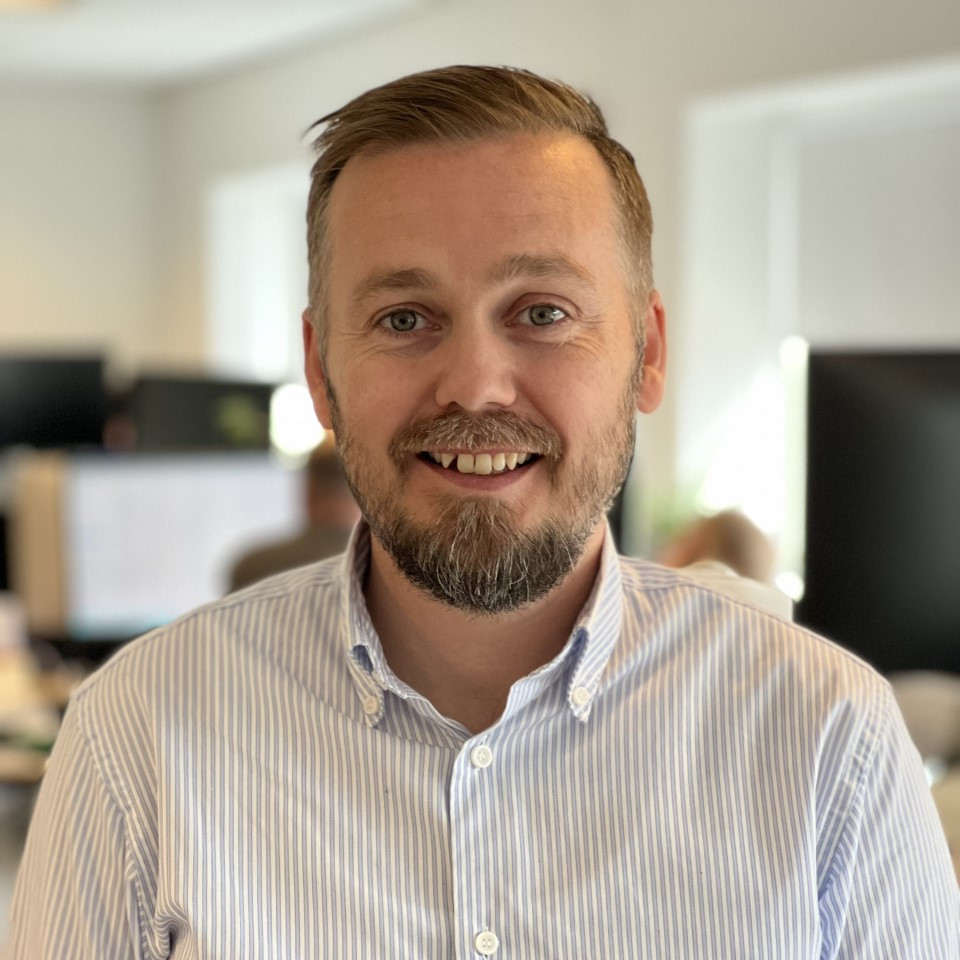
Understanding the benefits of CAN bus helps highlight why it has become such a vital part of modern technology. Here are some key advantages:
-
Cost-Effective:
-
Reducing the number of wires and connectors lowers manufacturing and maintenance costs.
-
-
Scalability:
-
CAN bus protocol can easily be expanded with new devices without needing major rewiring.
-
-
Error Detection:
-
CAN bus includes built-in error detection mechanisms, which help prevent communication failures and enhance system reliability.
-
CAN bus plays a crucial role in making modern technology more reliable, efficient, and cost-effective. Whether in your car, a factory, or a hospital, CAN bus protocol helps ensure that different components work together seamlessly. This interconnectedness is what makes complex systems function smoothly and reliably.
How Does CAN bus Work?
The basics of how the CAN bus works can help explain this important technology. Let’s break it down in simple terms.
CAN bus is a protocol that allows different parts of a machine or vehicle to communicate with each other through a common network. Imagine a group of people in a room having a conversation.
Instead of everyone shouting at once, they take turns speaking so everyone can hear and respond appropriately. This is similar to how CAN bus facilitates communication.
To understand how the CAN bus protocol works, it’s helpful to know about its key components:
-
Nodes: These are the devices or components connected to the CAN bus. Each node can send and receive messages. Examples include sensors, control units, and actuators.
-
Bus: This is the communication pathway that connects all the nodes. It’s like the highway that all the cars use.
-
Messages: Information is sent in the form of messages. These messages contain data and an identifier that tells the receiving nodes what kind of information is being sent.
Now, let’s look at how these components work together to make communication happen:
-
Message Sending: When a node needs to send information, it creates a message and puts it on the bus. For example, a sensor might send a message about the temperature to the control unit.
-
Message Receiving: All nodes connected to the bus receive the message, but only the intended recipient(s) process the information. The identifier in the message helps each node decide if the message is relevant to them.
-
Error Checking: CAN bus has a built-in error checking to ensure that messages are transmitted accurately. If a message is corrupted, it’s ignored and re-sent, ensuring reliable communication.
To make things clearer, let’s use some analogies:
The Nervous System Analogy
Step | Analogy | CAN bus Action | Outcome |
---|---|---|---|
1 | Think of the CAN bus protocol as the nervous system of a machine. | CAN bus sends messages between different electronic parts. | Makes sure everything works together smoothly. |
2 | Your brain sends signals through nerves to different parts of your body. | CAN bus acts like the nerves, sending messages between parts. | Helps different parts talk to each other. |
3 | Signals travel from the brain through nerves to different body parts. | Nodes (parts) send messages through the CAN bus to other nodes (parts). | Makes sure messages get where they need to go. |
4 | Each body part receives and responds to the brain’s signals. | Each node (part) gets the message it needs to do its job. | Keeps the whole system running smoothly together. |
The Highway Analogy
Step | Analogy | CAN bus Action | Outcome |
---|---|---|---|
1 | Picture a busy highway with multiple cars traveling to different destinations. | The highway represents the CAN bus with messages traveling. | The CAN bus is a shared path for all messages. |
2 | Each car (message) uses the same road (CAN bus) to get to its specific exit (device). | Messages travel along the CAN bus to reach their destinations. | Messages reach the correct part of the system. |
3 | Traffic rules (protocols) ensure that cars don’t crash and everyone reaches their destination safely. | Protocols manage the flow of messages to avoid collisions. | Ensures safe and reliable message delivery. |
A simple diagram can help visualize how CAN bus protocol works. Imagine a central line (the bus) with several small circles (nodes) connected to it. Arrows can show the direction of messages between nodes.
The CAN bus protocol is all about creating an efficient and reliable way for different parts of a machine or vehicle to communicate with each other. By using simple analogies and breaking down the components.
CAN bus Protocol
The CAN bus protocol is a set of rules that govern how data is transmitted between devices on the network. It ensures that all nodes can communicate efficiently without interference.
This protocol is essential for maintaining order and ensuring that messages are correctly prioritized and delivered.
In a CAN bus system, communication between devices is managed through a message-oriented protocol. Each device, or node, can send and receive messages. These messages contain an identifier that indicates their priority and the type of data they carry. The protocol allows for asynchronous transmission, meaning that nodes can send messages at any time without needing to be synchronized.
The CAN bus protocol is governed by several ISO standards, ensuring consistency and reliability across different implementations.
The primary standards are:
-
ISO 11898-1: Covers the data link layer and physical signaling.
-
ISO 11898-2: Defines the high-speed CAN physical layer.
-
ISO 11898-3: Defines the low-speed, fault-tolerant CAN physical layer.
These standards ensure that CAN bus systems are interoperable and meet specific performance and reliability criteria.
Next, we will explore the structure and function of a CAN message frame, a fundamental aspect of how data is transmitted and received in a CAN bus system.
CAN Message Frame
The CAN message frame is the format in which data is transmitted over the CAN bus.
Understanding the structure of this frame is crucial for grasping how the CAN bus system operates. A standard CAN message frame consist of several key fields:
Field | Description | Example |
---|---|---|
Start of Frame (SOF) | Indicates the beginning of the message. | 1 |
Identifier | A unique identifier that determines the priority of the message. | 11 (standard) / 29 (extended) |
Control Field | Contains information about the data length and type. | 6 |
Data Field | The actual data being transmitted, up to 8 bytes in length. | 0-64 |
CRC Field | The Cyclic Redundancy Check field, used for error detection. | 15 |
ACK Field | Acknowledgment field where receivers confirm the message was received correctly. | 2 |
End of Frame (EOF) | Indicates the end of the message. | 7 |
There are different types of CAN message frames, each serving a specific purpose:
Frame Type | Description | Example Data |
---|---|---|
Data Frame | The most common type, used to transmit data from one node to another. | Variable (depends on the data length) |
Remote Frame | Used by a node to request data from another node. | Same as Data Frame |
Error Frame | Sent when an error is detected in a message to notify all nodes on the bus. | 6-12 |
Overload Frame | Used to provide extra time for processing between data frames. | 6-12 |
Error frames and overload frames play a crucial role in maintaining the integrity of the communication on the CAN bus:
Field | Description | Example |
---|---|---|
Error Frame | When a node detects an error in a message, it sends an error frame to signal that the message should be discarded and retransmitted. This ensures that only valid data is accepted and acted upon. | 6-12 |
Overload Frame | These frames are used to delay the transmission of the next message, allowing nodes additional time to process the current data. This is particularly useful in high-traffic scenarios to prevent data loss. | 6-12 |
Next, we will look at the physical wiring of the CAN bus system, an essential aspect that affects its performance and reliability.
CAN bus Wiring
The physical layer of the CAN bus system is the foundation that determines how signals are transmitted between nodes. This layer includes the cables, connectors, and electrical specifications that ensure reliable data transmission.
In a typical CAN bus system, the most common wiring topology is a linear bus with nodes branching off along the main communication line. This configuration is simple, scalable, and efficient. Each node is connected to the bus through a pair of twisted wires, which helps to minimize electromagnetic interference.
Using twisted pair wiring is crucial in a CAN bus system. Twisting the wires together helps to cancel out electromagnetic interference (EMI) from external sources and ensures signal integrity over long distances. This is especially important in environments with high levels of electrical noise, such as automotive and industrial applications.
Termination resistors are essential components in a CAN bus system. They are placed at both ends of the bus to prevent signal reflections, which can cause data corruption and communication errors. Typically, a resistor value of 120 ohms is used for termination.
Types of CAN Bus systems
The CAN bus system can be classified into different types based on their speed and specific applications.
Understanding these types helps in selecting the appropriate CAN bus for various use cases.
High-Speed CAN Bus
The high-speed CAN bus is designed for applications requiring fast data transmission. Operating at speeds up to 1 Mbps, this type is commonly used in critical automotive systems where rapid communication between ECUs is essential, such as engine control, transmission, and safety systems.
Low-Speed/Fault-Tolerant CAN Bus
The low-speed or fault-tolerant CAN bus operates at speeds up to 125 Kbps. It is used in applications where communication speed is less critical but reliability is paramount. This type is ideal for non-critical vehicle systems like window controls, seat adjustment, and climate control. Its fault-tolerant nature ensures continued operation even if there is a wiring fault, making it highly reliable.
Applications of High-Speed and Low-Speed CAN Bus
-
High-Speed CAN Bus Applications: Primarily used in automotive systems for engine control units (ECUs), airbags, anti-lock braking systems (ABS), and other critical components that require fast and reliable data transmission.
-
Low-Speed/Fault-Tolerant CAN Bus Applications: Utilized in less critical vehicle functions such as power windows, seat adjustments, and infotainment systems. Its fault-tolerant capability ensures that these systems remain operational even if part of the network fails.
Next, we will explore the different types of CAN bus systems and their specific applications.
What is CAN bus Used For?
CAN bus is a versatile communication system used in many different industries. Its ability to streamline communication between various components makes it invaluable in several applications.
In the automotive industry, CAN bus is like the central nervous system of a car. It manages and coordinates multiple functions, ensuring that everything works together smoothly and instantly.
-
Example: When you press the brake pedal, the CAN bus protocol sends a message to the brake lights and other control systems. This ensures that your car stops safely and efficiently, and that the brake lights signal to other drivers.
In factories, CAN bus helps machines communicate effectively, leading to more efficient and reliable operations.
-
Example: On a production line, CAN bus allows different machines to share information. This coordination helps ensure that each machine operates correctly and that the entire production process runs smoothly.
In the medical field, CAN bus is used to ensure that devices work reliably and accurately, which is crucial for patient safety.
-
Example: In an MRI machine, CAN bus coordinates various sensors and control units to provide accurate imaging and diagnostics. It helps ensure that all parts of the machine are working in harmony, providing reliable results.
To bring this closer to home, think about some everyday uses:
-
In smart homes, CAN bus protocol can control lighting, heating, and security systems, making your home more efficient and convenient.
-
Buses and trains use CAN bus to manage various functions like doors, lighting, and passenger information systems, ensuring smooth and reliable operations.
-
Modern farming equipment uses CAN bus to coordinate between different parts of a tractor or harvester, improving efficiency and productivity.
"CAN bus is popular in so many areas because it’s dependable and efficient. Whether it’s in cars, factories, or medical devices, it helps different parts work together smoothly."
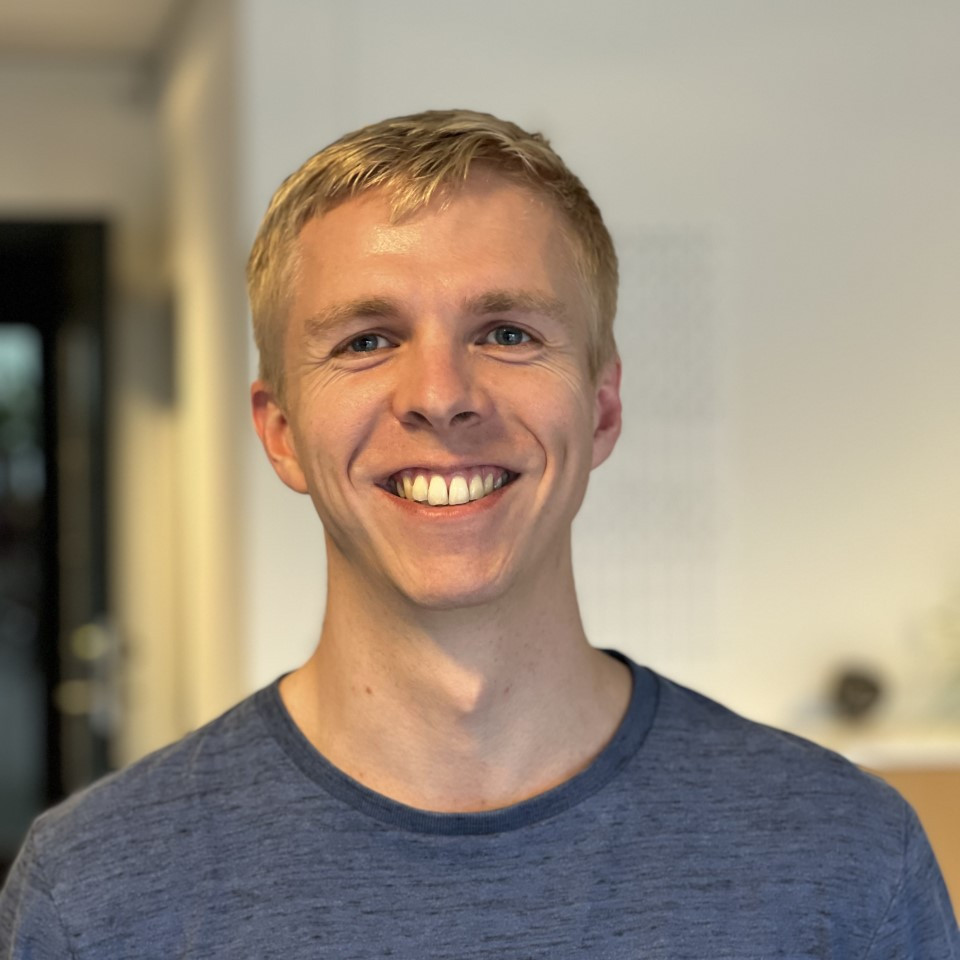
What are the Strength and Weakness of CAN bus?
Like any technology, the CAN bus protocol has its strengths and weaknesses. Understanding these can help you appreciate why it is widely used and where it might face challenges.
Strength of the CAN bus protocol
Feature | Explanation | Benefit |
---|---|---|
Cost-Effective | CAN bus reduces the amount of wiring needed, which lowers manufacturing and maintenance costs. | Fewer wires mean simpler installations and repairs, saving time and money. |
Reliability | CAN bus includes built-in error detection mechanisms. | These mechanisms help ensure that messages are transmitted accurately, making the system more reliable. |
Scalability | CAN bus protocol can be easily expanded by adding new devices without major changes to the existing setup. | This makes it easy to upgrade or expand systems as needed. |
Efficiency | CAN bus allows multiple messages to be sent over the same network without collisions. | This ensures smooth communication even in complex systems with many devices. |
Speed | CAN bus supports high-speed data transmission. | Fast communication is crucial for real-time applications like vehicle control systems. |
Weakness of the CAN bus protocol
Feature | Explanation | Drawback |
---|---|---|
Limited Distance | CAN bus is suitable for relatively short distances. | This limitation makes it less ideal for applications requiring long-range communication. |
Complexity in Large Systems | While CAN bus is scalable, managing very large networks can become complex. | More extensive systems may require additional management tools and techniques to maintain efficiency and reliability. |
Data Rate Limitations | Although CAN bus is fast, it has a maximum data rate that may not be sufficient for some high-bandwidth applications. | For applications requiring very high data rates, other communication systems might be more suitable. |
Interference | In environments with high electrical noise, CAN bus communication can be disrupted. | This requires additional shielding and error management strategies to ensure reliable communication. |
"CAN bus is super useful and reliable, but it’s important to know its limits. Understanding what it’s good at and where it might fall short helps you plan and build systems more effectively."
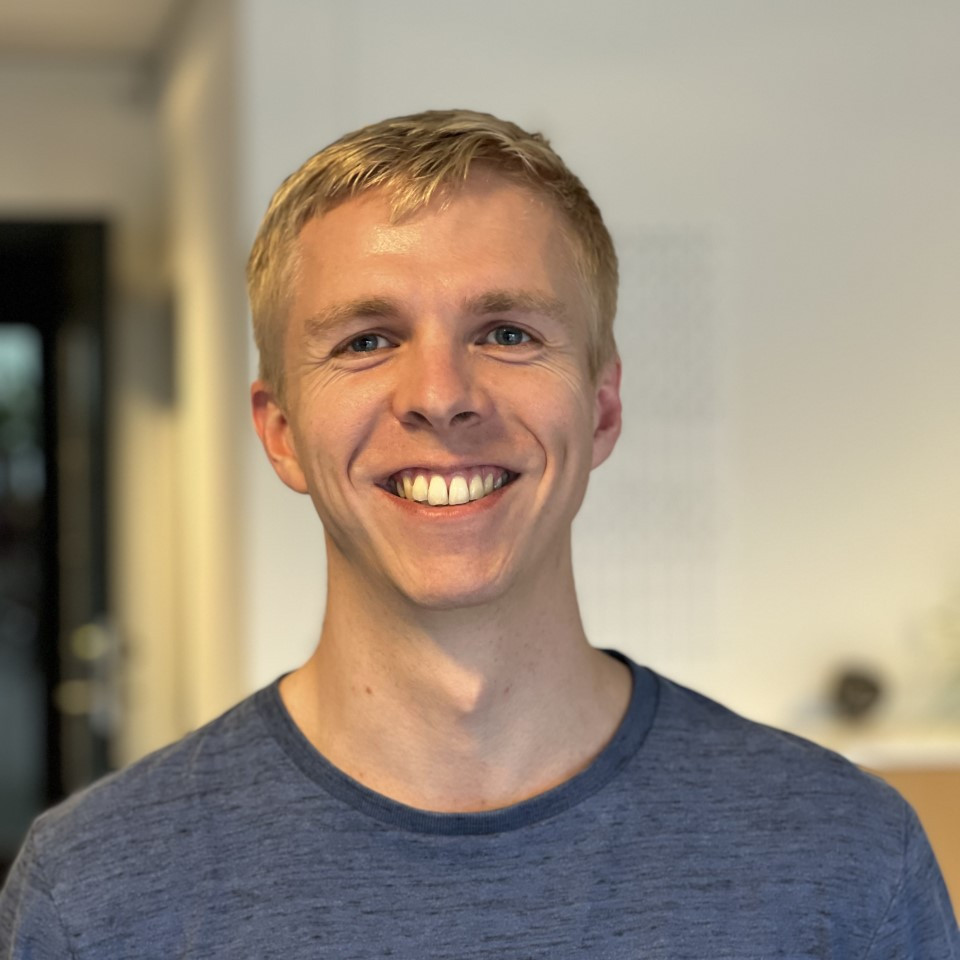
CAN bus offers many advantages, such as cost-effectiveness, reliability, scalability, efficiency, and speed, making it a popular choice in various industries. However, it also has some disadvantages, including limited distance, complexity in large systems, data rate limitations, and susceptibility to interference.
By weighing these pros and cons, you can better understand when and to take advantage of the CAN bus protocol.
Unlock the Full Potential of Your CAN Bus with AutoPi CAN-FD Pro
If you're looking to take your CAN Bus projects to the next level, the AutoPi CAN-FD Pro is the perfect tool for you.
Why Choose the AutoPi CAN-FD Pro?
The AutoPi CAN-FD Pro is engineered for professionals who demand precision, speed, and reliability. Here's why it's the ideal solution for your CAN Bus applications:
-
Supports CAN FD Protocol: The CAN-FD Pro offers support for both traditional CAN 2.0 and the faster CAN FD protocol, allowing for higher data rates and larger payloads—perfect for modern automotive, industrial, and embedded systems.
-
Enhanced Flexibility: With its user-friendly interface and versatile connectivity options, you can easily interface with different ECUs and integrate with your existing systems.
-
High-Speed Data Logging: Capture and analyze data at incredible speeds, ensuring you get the most accurate insights from your CAN network. The AutoPi CAN-FD Pro is built to handle high-frequency communication without compromising performance.
-
Customizable and Programmable: Tailor the device to meet your specific needs with programmable logic and advanced filtering capabilities. The AutoPi CAN-FD Pro supports real-time data processing, enabling you to fine-tune your system with ease.
-
Robust Software Ecosystem: Get access to a powerful software suite that allows for easy configuration, monitoring, and troubleshooting. With support for popular platforms like Python and Node.js, you can quickly develop and deploy custom solutions.
Perfect for a Wide Range of Applications
Whether you're working on automotive diagnostics, industrial automation, or prototyping new IoT devices, the AutoPi CAN-FD Pro is up to the challenge. It’s ideal for:
-
Vehicle Telematics: Monitor vehicle data, control systems, and troubleshoot in real-time.
-
Industrial Control Systems: Seamlessly integrate into automation setups for faster communication and reliable data exchange.
-
Embedded Systems: Build high-performance embedded applications with support for CAN Bus networks.
The Future of CAN bus
As technology advances, so does the role of CAN bus protocol in various applications. Here’s a look at what the future might hold for this essential communication system.
Emerging Trends
Increased Use in Autonomous Vehicles
With the rise of self-driving cars, the demand for reliable and efficient communication protocols like CAN bus is growing. CAN bus will likely play a crucial role in ensuring that various sensors and control units in autonomous vehicles communicate effectively, enhancing safety and performance.
Integration with IoT
As more devices become connected through the Internet of Things, CAN bus can provide a robust communication backbone. This integration will allow for smarter, more connected systems in homes, industries, and cities, improving efficiency and functionality.
Advancements in CAN FD (Flexible Data-rate)
CAN FD is an enhanced version of the traditional CAN bus that supports higher data rates and increased data payload. With CAN FD, systems can handle more complex data and faster communication, making it suitable for advanced applications in automotive and industrial fields.
Potential Innovations
Enhanced Security Features
As systems become more connected, the need for secure communication increases. Future CAN bus protocol may include advanced encryption and authentication methods to protect against cyber threats.
Greater Interoperability
Ensuring that CAN bus can easily integrate with other communication protocols will be essential. Development of hybrid systems that combine CAN bus with other technologies (like Automotive Ethernet) to enhance overall system capabilities.
Energy Efficiency Improvements
Reducing energy consumption is a priority for many industries. Future iterations of CAN bus may focus on minimizing power usage, making them more suitable for energy-sensitive applications.
The evolution of CAN bus technology promises exciting advancements and wider applications. As it adapts to meet the demands of modern technology, CAN bus will continue to be a fundamental part of systems ranging from autonomous vehicles to smart cities. By staying ahead of emerging trends and potential innovations, CAN bus will remain a reliable and efficient communication standard for years to come.
Conclusion
We’ve journeyed through the basics of the CAN bus protocol, its importance, how it works, its applications, the pros and cons, and its future prospects. Here’s a quick recap:
-
What is CAN bus?: It’s a communication system that allows different parts of a machine or vehicle to talk to each other efficiently.
-
Importance: CAN bus protocol simplifies complex systems, enhances reliability, and is crucial in many industries like automotive, industrial machinery, and medical devices.
-
How It Works: Using analogies like the nervous system and highways, we broke down how CAN bus manages communication between various components.
-
Applications: From cars to factories to medical devices, CAN bus is integral to many technologies we rely on daily.
-
Pros and Cons: While it offers many advantages like cost-effectiveness and reliability, it also has limitations such as distance constraints and complexity in large systems.
-
Future: The future looks promising with trends like autonomous vehicles, IoT integration, and advancements like CAN FD.
Final Thoughts
CAN bus is an essential technology that continues to evolve and adapt to new challenges and applications. Whether you’re in the automotive industry, working with industrial machinery, or dealing with medical devices, understanding the CAN bus protocol can provide valuable insights into how modern systems communicate and operate efficiently.
Ready to learn more or need help implementing CAN bus in your projects? Contact our experts today to see how we can assist you in leveraging CAN bus technology for your specific needs.
Further Readings
For those interested in diving deeper into the world of CAN bus, here are some recommended resources:
By exploring these resources, you can deepen your understanding of CAN bus and stay updated on the latest developments and best practices in the field.